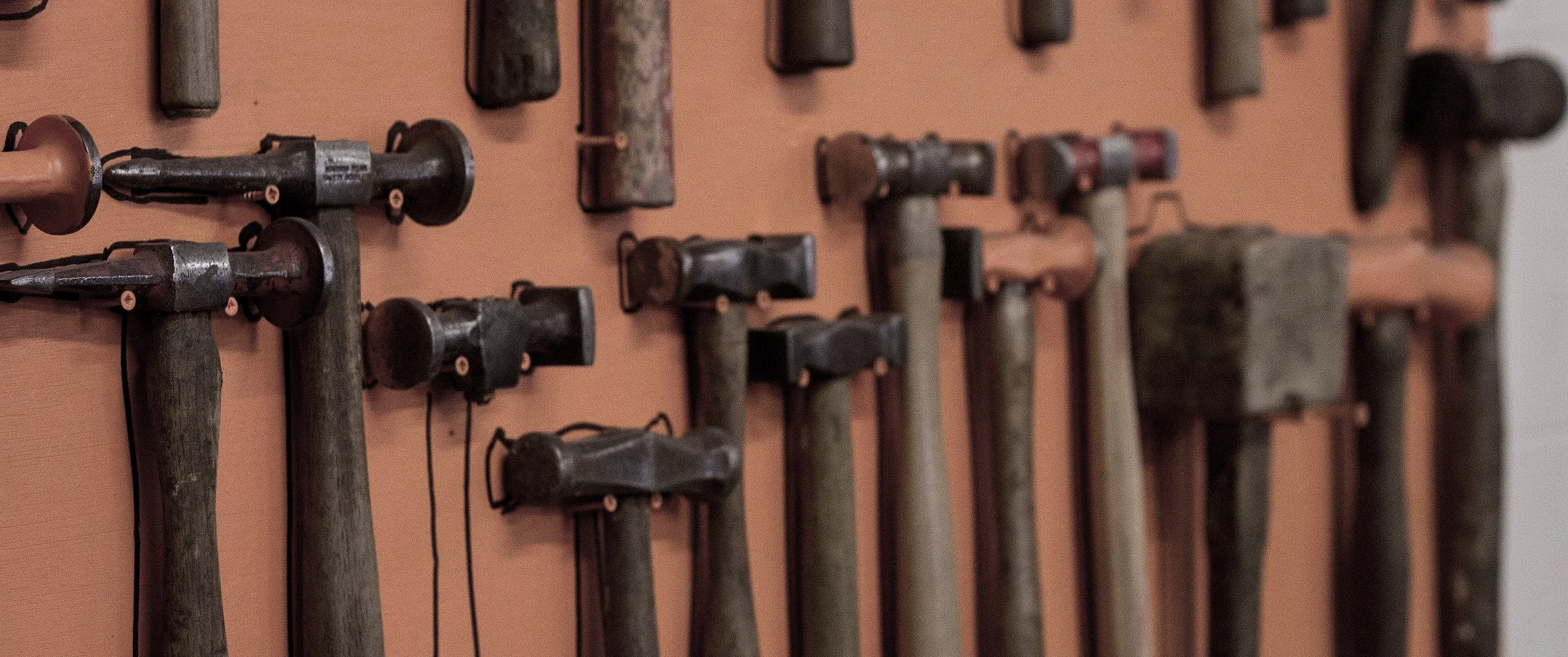
The Process
The build process starts with the buck on the ground to allow for easier access. When all the panels have been shaped, we install the buck on the platform before fitting the panels to the floors and sill section.
Once we have proved the construction, we do a full strip down before sending the Land Rover and the chassis to paint. While the vehicle is away at paint, we start working on the components of the interior.
When both the aluminium frame and the skin of the habitation pod are complete, we begin working on the interior.
We use a composite thermal barrier to prevent cold bridging, and spray 60 mm of closed cell foam. This provides incredible insulation as well as an effective vapour barrier to prevent condensation from the aluminium skin.
We make a 3D model in CAD to allow us to make a plywood buck: a removable wooden template used to shape the frame and bodywork.
This process allows us to adjust and tailor the body of the habitation pod, and to adapt our pods to any platform. This means we are not confined to the Defender or this size and shape of pod.
After all the panels have been fitted and fixed to the template, we strip the panels and framework down to allow removal of the the buck. The next step is a full dry fit, which involves assembling all the metal components of the frame and skin, to construct the final form of the pod.
Once the platform is back from paint, we move to the final stage of habitation pod installation, which involves all components being glued, sealed and riveted, using over 2000 solid rivets.
The final stage of the habitation pod construction is the internal skin, which is built from bamboo for its strength to weight ratio and aesthetics.